The mechanical engineering industry is crucial in designing, developing, and producing various products and systems. From automobiles and aircraft to medical devices and consumer products, mechanical engineers use their skills to create innovative solutions to real-world problems.
Additive manufacturing, or more commonly known as 3D printing, has revolutionized the way mechanical engineers work. This process involves using computer-aided design (CAD) software to create digital models of objects, which are then built layer by layer using materials such as plastic, metal, or ceramic.
One material that has gained popularity in the mechanical engineering industry is titanium. Titanium 3D printing allows mechanical engineers to produce parts and prototypes with the desired properties of titanium while also taking advantage of the customization capabilities of 3D printing.
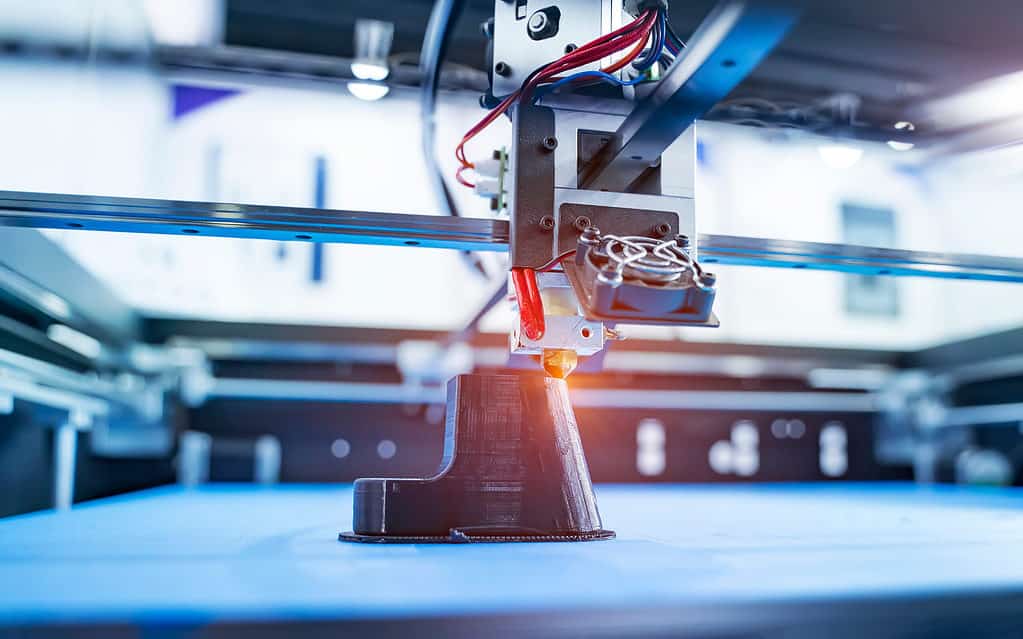
Read on to learn more about the role of 3D printing in the mechanical industry.
History Of 3D Printing
As early as the 1980s, the mechanical engineering industry has already begun using 3D printing technology. Initially, it was mainly used for prototyping and producing small specialized parts. However, as technology improved and evolved, it is now increasingly adopted for various applications in the industry.
One key factor driving the evolution of 3D printing technology has been the development of new materials and processes, including the ability to 3D print with metals like titanium, stainless steel, and aluminum.
Advantages Of Using 3D Printing
The mechanical engineering industry can benefit from several advantages when using 3D printing. These advantages include the following.
1. Increased Design Flexibility And Customization
With 3D printing, engineers can create complex geometries and intricate designs that would be impossible to produce using traditional manufacturing methods. It allows greater creativity and customization in product design and in creating one-off prototypes or low-volume production runs without incurring the costs associated with conventional manufacturing methods.
2. Reduced Production Times And Cost Savings
Traditional manufacturing methods, such as machining or injection molding, require extensive setup and preparation before production can begin. It can lead to long lead times and high production costs. In contrast, 3D printing allows rapid prototyping and production with the ability to produce parts on-demand without the need for expensive tooling or setup. It reduces production times and minimizes costs through reduced material waste and lower energy consumption.
3. Improved Product Performance And Reliability
Since 3D printing allows the creation of complex geometries and precise internal structures, it can produce parts with improved mechanical properties and performance. Additionally, 3D-printed parts can also be designed with improved structural integrity, reducing the risk of failure and increasing the overall reliability of the finished product.
Applications Of 3D Printing
There are numerous ways in which 3D printing has been applied in the mechanical engineering industry. Some of these applications include the following.
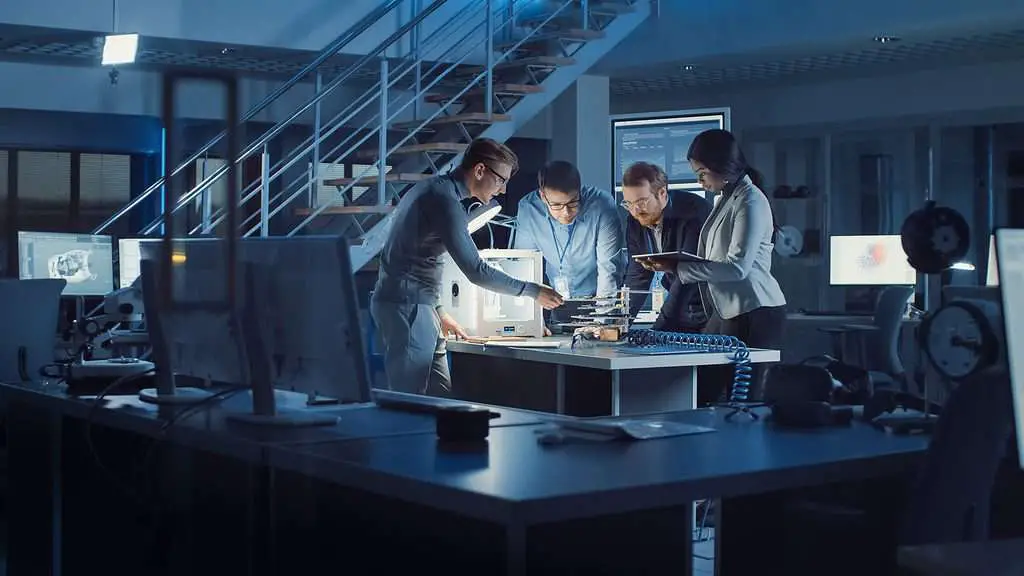
1. Prototyping In Product Development
Using 3D printers, engineers or designers can build prototypes layer by layer using various materials, including plastics, metals, and ceramics. It eliminates the need for molds or tooling and allows for faster iteration and testing of designs.
Notably, a company developing a new automotive component can use 3D printing to produce prototypes for testing and evaluation. In the aerospace industry, 3D printing delivers complex and lightweight aircraft and rocket component prototypes. In medical device manufacturing, 3D printing has been used to create surgical instruments and implant prototypes.
2. Custom And Complex Parts Production
There are numerous examples of 3D printing used by various companies to produce custom and complex parts. A company producing custom-fit ski boots is one great example. The company can improve comfort and performance by using 3D printing to create precise and personalized footbeds for each customer.
Another example is a manufacturer of hydraulic systems for heavy machinery, which uses 3D printing to produce custom manifolds and valve bodies with complex internal geometries. It reduces lead times and costs compared to traditional manufacturing methods.
3. Repair And Maintenance Of Mechanical Equipment
Repairing and maintaining manufacturing equipment can be a time-consuming and costly process. It often requires sourcing and ordering replacement parts, which can take time to arrive and may only sometimes be in stock. One solution to this problem is the use of 3D printing technology.
A construction equipment manufacturer can use 3D printing to produce a replacement part for a hydraulic excavator that’s no longer in production. With 3D printers, the manufacturer can design and print the part, saving time and money on sourcing and shipping costs.
In addition, a manufacturer of industrial pumps can use 3D printing to produce replacement parts for older or hard-to-find models, reducing the need for inventory and enabling the continued operation of older equipment.
Conclusion
Overall, 3D printing has played a significant role in the mechanical engineering industry, offering a range of benefits and industrial applications. Not only does it increase design flexibility and customization but it also improves product performance and reliability without having to rely on costly processes. As technology evolves, there will be even greater adoption and integration of 3D printing in this industry.
nice article.thanks