Today we will learn about investment casting working process, application, advantages and disadvantages with its diagram. Investment casting is one of the most important types of casting process which gives high accuracy and surface finish. This process uses wax pattern to create mould. The wax pattern dipped into a refectory material which makes a shell outside the pattern. Now the refectory material heated which melt down the wax and taken out. The molten metal poured into this refectory mould and allows to solidify. When the metal solidified, the ceramic shell broken and casting is removed from it. This casting process gives high surface finish and good dimensional accuracy compare to other casting process. It is mostly used to cast complex shapes like turbine blade etc.
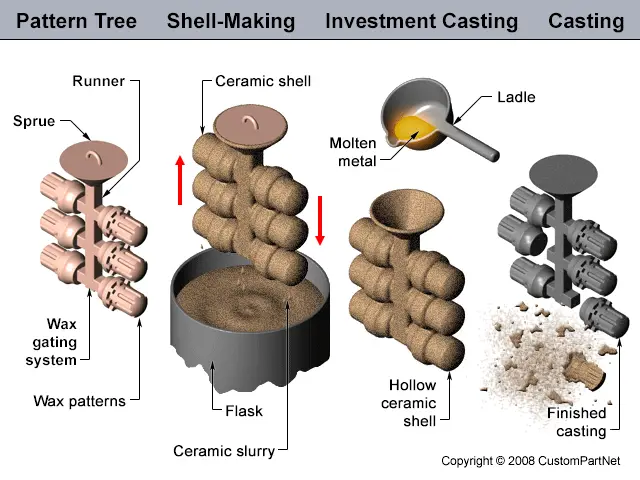
Investment Casting Process:
Working:
Its working can be summarized into following point.
- In the beginning of this process, a wax pattern created together with its gating system into a die cavity.
- A tree is prepared from number of such pattern fixed to a wax or plastic runner bar with a suitable ceramic cup to act as pouring basin.
- The tree is then dipped into ceramic slurry (refectory material). This enables the formation of self-supporting ceramic shell mould to be formed around the wax assembly.
- The ceramic shell mould is then heated so that the wax melts and flows out leaving a precise mould cavity.
- The shell is fired between 850 degree centigrade and 1000 degree centigrade to eliminate all the wax and give more strength to the mould.
- The molten metal is poured into the mould while it is still hot and cluster of castings is obtained.
- At the end, ceramic mould is broken and removed the casting.
Application:
- It is used to cast small size casting having intricate shape.
- These are used to form jewelry surgical equipment.
- It is used to cast complex shapes like turbine blades, bolt and trigger for fire arm etc.
Advantages and Disadvantages:
Advantages:
- High melting point alloys can be cast by this process.
- It gives high surface finish and dimensional accuracy.
- Complex shapes which are difficult to produce by any other casting method can be produce by investment casting because pattern is withdrawn by melting it.
- Thin section with fine details can be cast by this process.
- More than one part can be cast simultaneously.
Disadvantages:
- The process is normally limited by the size and mass of the casting.
- It is expressive compare to other casting processes.
This is all about investment casting process working, application, advantages and disadvantages. If you have any query regarding this article, ask by commenting. If you like this article, don’t forget to share it on social networks. Subscribe our website for more interesting articles.